In general, the rubber roller coating process means that the customer provides the rubber roller iron core. The rubber roller factory is responsible for rubberizing and grinding the rubber roller iron core, and grinding the rubber roller into the required size, color, hardness, etc. according to the customer's requirements. . Rubber roller processing and lagging needs to go through the following processes:
1. Cleaning the rubber roller iron core: If it is a new rubber roller iron core, the oil stain on the surface of the iron core needs to be cleaned with a cleaning agent; if it is an old rubber roller iron core, the outer layer of the old rubber roller needs to be removed. At the same time, use the cleaning agent to clean the remaining glue on the surface of the iron core.
2. Rough surface treatment of the iron core of the industrial rubber roller: roughen the surface of the iron core of the rubber roller to increase the bonding area between the iron core surface of the rubber roller and the rubber.
3. Sandblasting treatment: Sandblast the rough treated rubber roller core, and sandblasting will select different types of sand according to the material of the rubber roller core for sandblasting. The purpose of sandblasting is to make the surface of the rubber roller rougher, and the glue and the iron core will be better bonded after rubberizing.
4. Lagging: The iron core of the rubber roller after the above treatment is covered according to the customer's requirements, and different covering materials meet different requirements. The pressure resistance is good, and the high temperature resistance of the silica gel is good.
5. Rubber roller vulcanization: The rubber roller generally needs 10-15 hours of vulcanization time after vulcanization. After vulcanization, the iron core of the rubber roller and the rubber cover will be closely bonded, and a rubberized rubber roller will be formed.
6. Cots grinding: Grind according to the size and shape required by customers. When some customers have higher requirements on the surface of the rubber rollers, it is necessary to use a CNC grinder to mirror the rubber rollers.
After the above 6 processes, the rubber roller encapsulation processing is completed. After ten years of development, Dongguan Keyi Rubber Roller Factory can encapsulate rubber rollers with a diameter of 10MM-1 meter. The rubber, polyurethane or silicone rubber can be selected according to the use of the rubber roller. The products are sold at home and abroad, and have been well received and recognized by our customers.
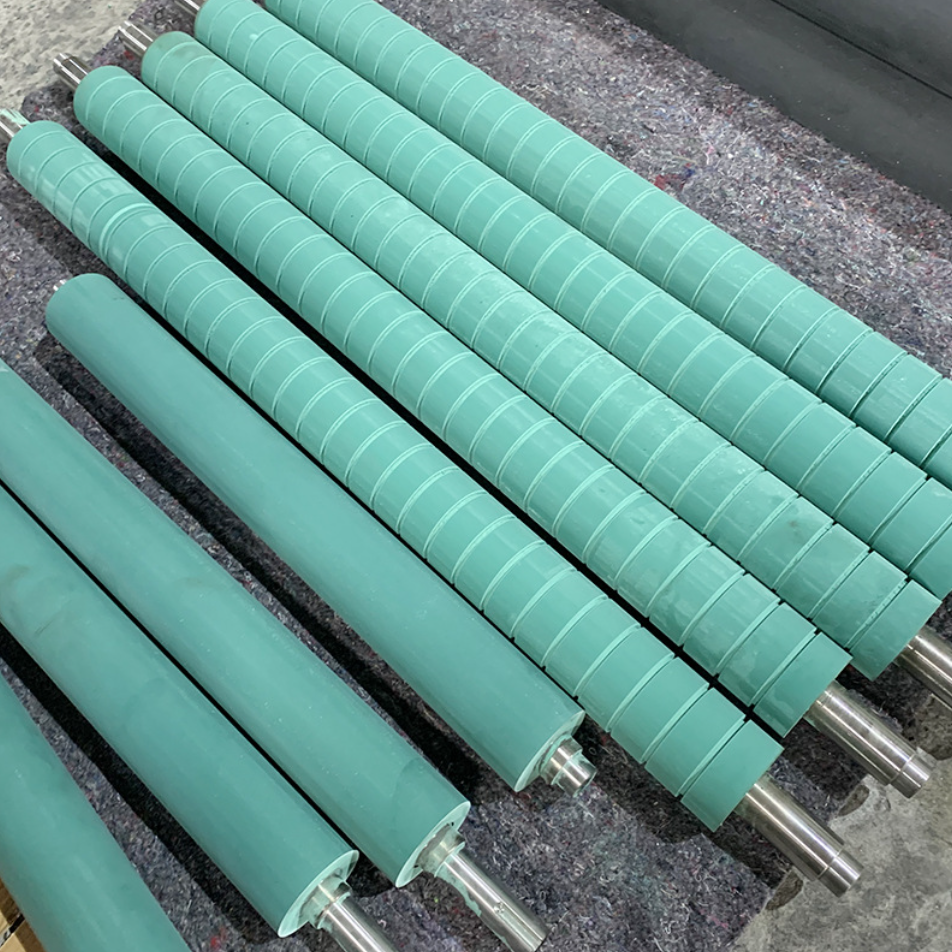
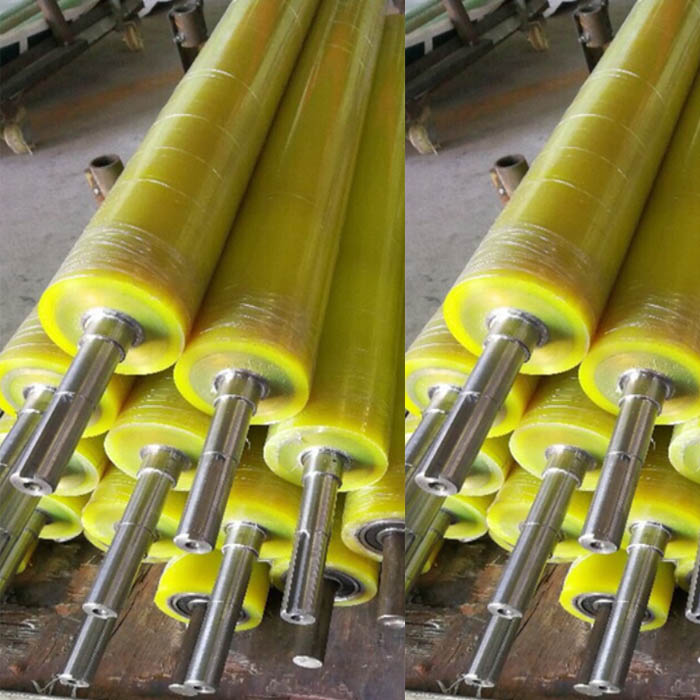
In recent years, due to the rapid development of various industries, the production equipment has been continuous, fully automated and refined. The rollers play a very important role in it. The quality requirements of customers for rubber rollers are also more stringent.
DECAI has been engaged in the professional manufacture of rubber rollers for 50 years. It has advanced experience in the development of rubber rollers, and cooperates with advanced production technology and exclusive formula to produce high-quality rubber rollers.
The company gathers professionals from all walks of life and rich on-site experience, with a meticulous and practical business philosophy, according to the needs of customers to "prescribe the right medicine" to help improve customers' production capacity and product quality, and develop high-temperature, solvent-resistant, acid-resistant Alkali, oil-resistant, wear-resistant and other material rollers. Now it is widely used in steel industry, plastic industry, plywood industry, stationery industry, leather industry, textile industry and other industries, and it is well received in the market.
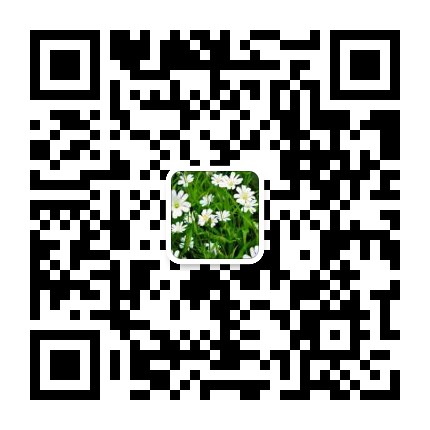
Post time: Jan-17-2022