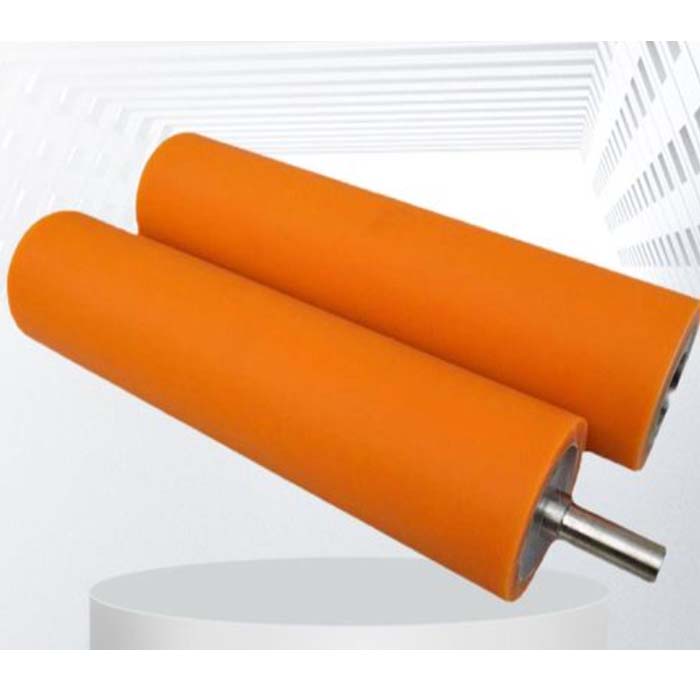
The rubber roller is a roller-shaped product made of metal or other materials as the core and the outer rubber is vulcanized. The rubber roller can be customized according to the user's needs, with a hardness ranging from 50-99 degrees, any color can be selected, and the temperature resistance is from -100 degrees to 300 degrees. Cots with various properties can be produced because of the different formulations of the rubber rollers.
The production process of rubber rollers generally includes 4 steps:
1. Iron core of rubber roller
2. Rubber Coated for rubber roller
3. Rubber roller vulcanization
4. Rubber roller grinding.
Therefore, please give us 3-5 days of processing time after you place the order. Dear friends, please do not ask us to deliver the goods the next day after placing an order, because the rubber roller manufacturing itself requires such a long process time, and any rubber roller factory will It is the same, it is impossible to deliver the next day. If you are in a hurry, please contact our customer service to explain the situation when placing an order. We will arrange production as soon as possible, and it will take 3 days at the earliest. According to the quantity of your order, users with large quantity can deliver in batches.
Classification of rubber rollers
1- According to the application, it can be divided into papermaking rubber rollers, printing and dyeing rubber rollers, printing rubber rollers, hulling rubber rollers, metallurgical rubber rollers and mimeograph rubber rollers, etc.;
2-According to the surface shape, it can be divided into flat roller and pattern rubber roller;
3- According to the material, it can be divided into butyl rubber roller, nitrile rubber roller, polyurethane rubber roller and silicone rubber roller, etc.
It is generally composed of outer rubber, hard rubber layer, metal core, roll neck and vent hole.
In what environment and performance do the rubber rollers you use need to be used? Keyi Rubber Roller Factory will choose the appropriate covering material for covering according to your requirements. The key is that you use the right one. Save you a lot of time and help your production create more value!
What industry is the rubber roller used in
Cots are mainly used in papermaking, printing and dyeing, printing, grain processing, metallurgy, plastic processing and other industries.
The printing industry mainly uses printing rubber rollers, and printing rubber rollers generally use rubber as the covering material;
The metallurgical industry mainly uses polyurethane rubber rollers, because polyurethane rubber rollers have high wear resistance, which are more wear-resistant than rubber rubber rollers;
Printing and dyeing rubber rollers generally require that the rubber rollers need to have better ink resistance and corrosion resistance;
Silicone rollers are generally used in high temperature environments.
How to use the rubber roller
1. The newly cast rubber rollers should not be put into use immediately. Since the internal structure of the newly cast rubber rollers is not stable enough, if they are put into use immediately, the service life will be reduced easily. Therefore, the new rubber rollers that have just come out of the cylinder should be placed for a period of time to keep the rubber rollers in a relatively stable state after contacting the temperature and humidity of the external environment. This can increase the toughness of the colloid, thereby improving the durability.
2. Correct storage of idle rubber rollers. After cleaning, the rubber rollers to be used should be sealed with plastic film and placed on the rubber roller rack. Do not pile up a few casually or lean against the wall to avoid Make the colloid suffer undue loss. During the transportation of waste rubber rollers to processing and casting, do not throw them indiscriminately or press them heavily, and keep the roller cores from eccentricity and bending to ensure the normal use of the roller cores.
3. Cots and bearings should be well lubricated. We know that the accuracy of the cots and bearings will directly affect the ink transfer and ink distribution. If the lubrication is poor, it will cause the wear and gap of the shaft head of the rubber roller, the bearing, and the gap, which will inevitably lead to the disadvantage of uneven printing ink color. At the same time, printing bar marks will also be caused by bad conditions such as rubber jumping and slipping. Therefore, lubricating oil should be frequently added to the shaft head and bearing of the rubber roller at ordinary times to prevent the normal use of the rubber roller from wear and tear on the machine parts and ensure the printing quality.
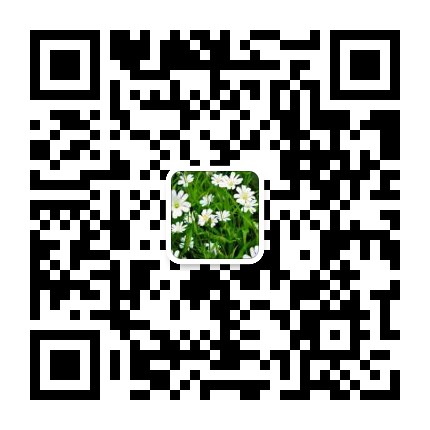
Post time: Dec-12-2022