The general faults and troubleshooting methods in the operation of the husking rubber roller are as follows:

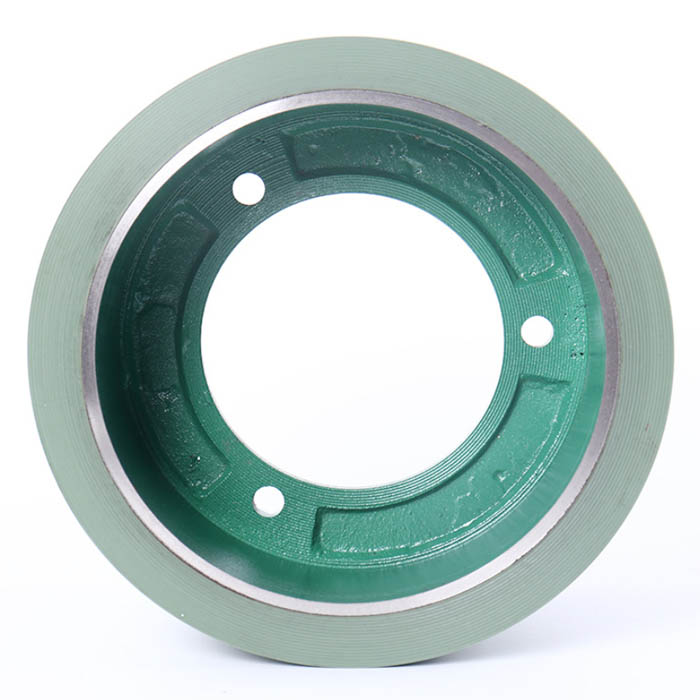
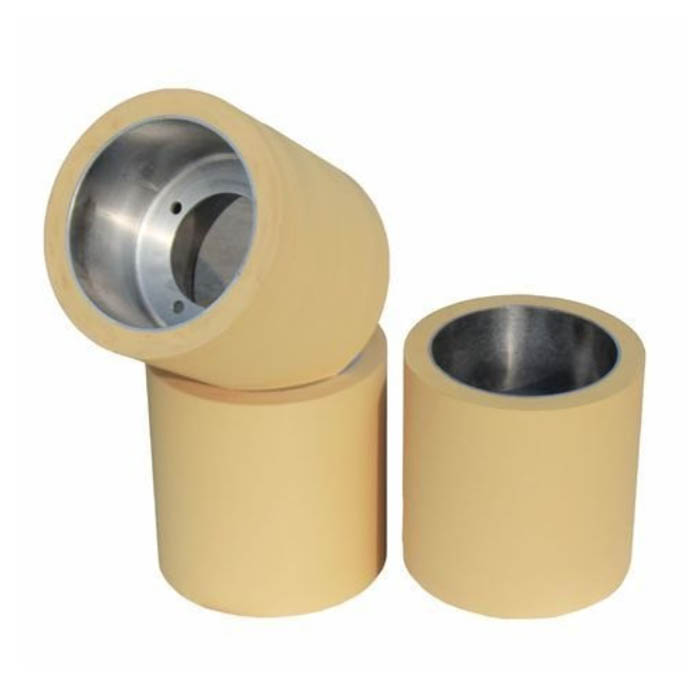
Rubber roller stuck
1. Uneven blanking 1. Adjust whether the accelerating flow plate is smooth and whether there are impurities stuck in the blanking material.
2. The raw materials contain too much impurities, strengthen the cleaning and removal of impurities and the maintenance management of the equipment.
3. The blanking material is directly impacted to adjust and accelerate the angle of the dripping plate.
4. The wear-resistant sundries have been mixed into the two-roller shaft (not easy to detect), open the cage every shift and check, clean or enlarge the rolling distance to let it flow out.
5. The back-hulled rice is on one side, and the feeding of the back-hulled rice is adjusted evenly.
Roller size head
1. The axes of the two rollers are not parallel, and the axle seat is adjusted slightly until the axes of the rubber rollers are parallel.
2. The flow rate of the feed flow plate is more on one side and less on the other side, adjust the feeding uniformity, accelerate the flow coefficient of the flow plate, and adjust the position of the heavy thallium.
3. The rolling distance is large on one side and small on the other, adjust the wheelbase and keep the axes parallel.
4. Return the rice to one side and adjust the rubber roller to keep it parallel to keep the rice feeding evenly.
5. The weight of the pressed lumps at both ends is uneven; adjust the pressed lumps to equal weight
6. Eliminate the deviation of the board, adjust the angle of the board
The husker vibrates too much
1. The deformation of the rubber roller shaft produces radial runout. Check the roller shaft before installation. Correct the balance.
2. The rubber roller is out of round
(1). Perform a static valley balance test on the rubber roller before installation (it has been tested before leaving the factory).
(2). Properly enlarge the wheelbase and debug it after a certain period of time.
(3). Turn on the lathe. Or return to the factory for processing
(4). Add a thin gasket on the edge of the two-cone hole.
Excessive wear of the rubber roller
1. The speed difference between the two rubber rollers is too high, and the appropriate line speed difference is controlled at 5-6m/s.
2. The pressure between the two rubber rollers is too large and the rolling distance is too tight; reduce the thallium weight or adjust the rolling distance
3. Grooving, flashing, uneven cutting.
4. The efficiency of cleaning equipment is low, the inspection management is accelerated, and the efficiency of impurity removal is improved.
5. The impurity and moisture content of paddy is too high; choose high wear-resistant rubber roller
6. The working temperature of the rubber roller is too high; the hardness of the rubber roller is not enough, and other high wear-resistant rubber rollers need to be replaced
low roughness
1. If the surface of the rubber roller is uneven, turn it on a lathe, or return it to the factory for reprocessing.
2. The gap between the two rubber rollers is too large, adjust the gap between 0.5-0.8mm.
3. The speed difference between the two rubber rollers is too high, and the appropriate line speed difference is controlled at 5-6m/s.
rubber roller edge
1. The lengths of the two rollers are not aligned when they are installed, adjust the optional rubber rollers and install them neatly at both ends.
2. The length of the rubber roller itself is wrong, replace the rubber roller
Rubber roller pattern
1. Uneven feeding and friction between rubber rollers
(1). Adjust the rubber roller to keep it parallel;
(2). Adjust the blanking;
(3). Keep the distance between the rubber rollers
Roller de-cored, burst, and disintegrated
1. The quality of the rubber roller is not good; if the quality of the rubber roller is not good, replace the rubber roller
2. The rubber roller is aging; stop using
3. The direct friction time of the two rollers is too long, adjust the gap
Deformation of the rubber roller
1 Improper storage, local aging or melting; replace the rubber roller
2. The static balance calibration is inaccurate and the position of the counterweight is not correct; turn on the lathe, or return to the factory for reprocessing
3. The working temperature of the rubber roller is too high, the quality of the rubber roller is poor, and other rubber rollers need to be replaced
4. When the rice shelling is difficult, the continuous working time is too long, and the hardness of the rubber roller is not enough, and other high wear-resistant rubber rollers need to be replaced.
Roller wear too fast
1. The line speed difference between the two rollers is too large, and the shelling rate is too high; adjust the line speed
2. The pressure between the rolls is too large and the rolling distance is too tight; adjust the rolling distance
3. The impurity and moisture content of paddy is too high; choose high wear-resistant rubber roller
4. The working temperature of the rubber roller is too high; the hardness of the rubber roller is not enough, and other high wear-resistant rubber rollers need to be replaced
5. The hardness of the rubber roller is too high, and the rubber roller with slightly lower hardness or moderate hardness is selected.
Vertical and horizontal ripples on the surface of the rubber roller
1 The downflow of the rice is not smooth; pay attention to adjusting the downflow of the rice
2. Improper selection of line speed difference or rolling distance; adjust line speed difference or rolling distance
3. The rubber roller is loose; adjust the rubber roller
4. The static balance is inaccurate, adjust the static balance or return to the factory for processing
The working temperature of the rubber roller is too high:
1. Poor ventilation; expand the types of ventilation
2. The line speed difference is too large, the pressure between the rolls is too large, adjust the line speed difference
3. The roughness of the hulled valley is too high; reduce the roughness of the hulled valley
4. The two rollers are in direct contact, adjust the distance between the rubber rollers
3. The surface of the rubber roller is bad:
(1) Net. Grain contains hard impurities; choose other rice or stop to find hard impurities or objects
(2). The line speed difference is too large, the rolling distance is too small or the pressing lump is too heavy; adjust the speed difference, rolling distance, pressing lump at the same time
(3). The husker vibrates seriously; adjust the balance of the rubber roller
(4). The water content of the rice is too high, so choose other rice or sun-dried before processing.
The middle convex or middle concave of the rubber roller:
1. The flow layer is concentrated or uneven; adjust the feeding method to make it evenly dispersed
2. If the dripping board is uneven, adjust the dripping board
3. The gate is worn or crescent-shaped; replace the gate
4. The big and small ends of the rubber roller, only pay attention to the big end, and the two ends of the rubber roller at the same time
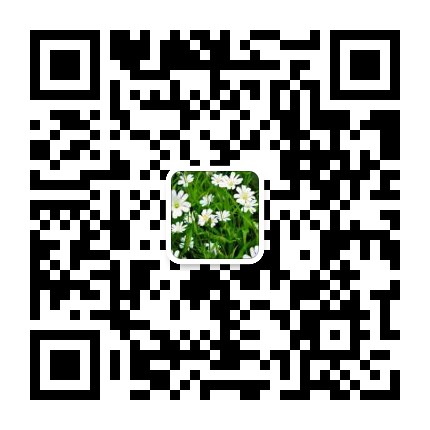
Post time: Jun-13-2022