The ink transfer of the anilox roller is quantitative, but how is it in practical use?
Since the function of the rubber roller is to squeeze out the ink on the surface of the anilox roller, its pressure can be slightly larger.
If the line number of the anilox roller used is too high, when printing color blocks and large characters, when the amount of ink transfer is not enough, the operator often adopts the method of increasing the gap between the rubber roller and the anilox roller to increase the amount of ink supply. In this way, a gap is created between the rubber roller and the anilox roller. The generation of the gap loses the quantitative ink supply function of the anilox roller.
Therefore, the use of anilox rollers must have the concept of "quantitative" ink supply. The amount of ink transfer cannot be adjusted by gaps. If there are gaps, the amount of ink cannot be controlled well. If the color blocks are not flat, streaks will appear; .
If the ink on the screen wall of the anilox roller cannot be squeezed out under the normal contact state between the rubber roller and the anilox roller, it means that the viscosity of the ink is too high, and the viscosity of the ink should be adjusted.
Notes in use:
Usually, the rubber roller is rotated with the anilox roller through surface contact to generate friction, but the linear speed cannot be the same. why?
Because only the linear speed of the surface of the rubber roller is slightly lower than that of the anilox roller, the excess ink on the surface of the anilox roller can be wiped off.
Since the hardness of the anilox roller is much higher than that of the rubber roller, it is forbidden to run "dry grinding" in the state of no water and no ink in actual use, otherwise the rubber roller will be damaged in a very short time.
When using rubber rollers, for repeated orders, it is necessary to control the speed of the vehicle, because the amount of ink increases with the increase of the vehicle speed, and the higher the vehicle speed, the thicker the ink.
After get off work or not in use for a long time, the rubber roller should be separated from the anilox roller to avoid pressure damage to the rubber roller and uneven ink transfer lines.
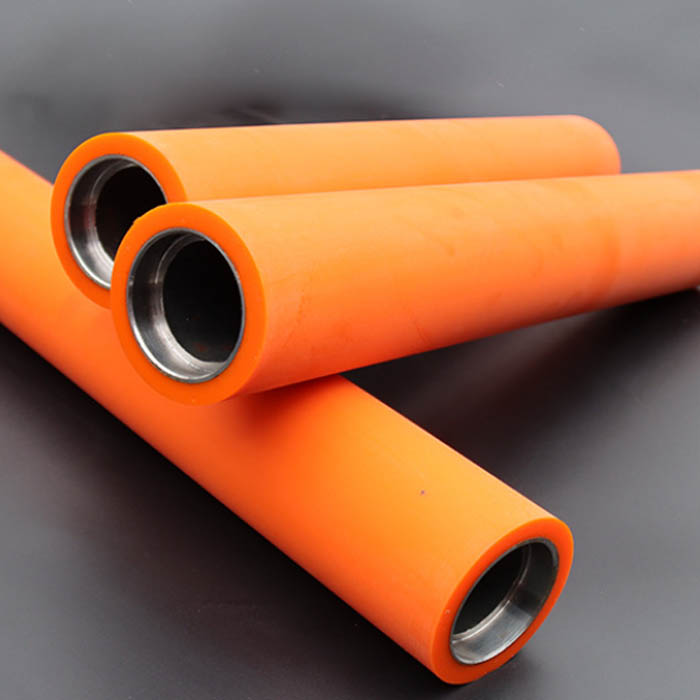
The bearing and shaft head structure inside the rubber roller is very precise, and a slight difference will directly affect the use effect. If the lubrication of the bearing and the shaft head is not very good, it is easy to cause wear and tear, and it will seriously affect the quality of the rubber roller, thereby affecting the quality of the product.
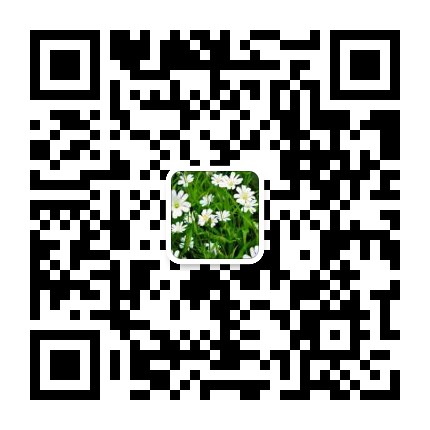
Post time: Feb-21-2022