Due to the rapid development of office equipment for various purposes in recent years, a large number of rubber rollers with different performance requirements have also been used.
Rubber rollers can generally be divided into five categories according to their functions:
①Glue roller-used for painting, ink coating, etc.;
②Squeeze rubber rollers-used for extruders, squeezers, wipers, etc.;
⑧ Transfer rubber roller-used for guide, turntable support, roller, accumulator;
④Buffer rollers-used for printing, pressing rollers, backing rollers, supporting rollers, printing rollers, etc.;
⑤ Transmission rubber rollers-used for roller tensioning devices, pressing equipment, pinch rollers, and dragging devices.
In addition, some roller ends are included in the basic classification, such as cleaning rollers.
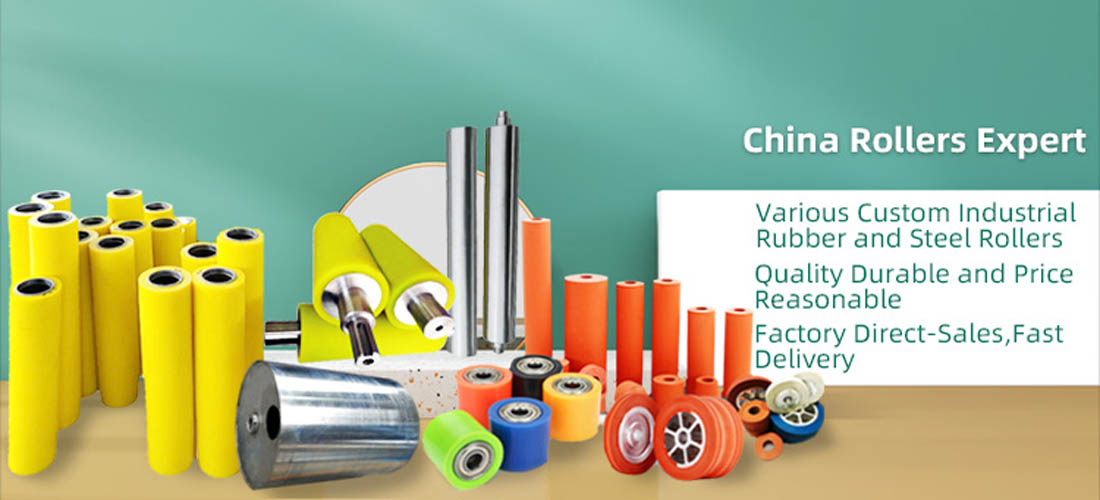

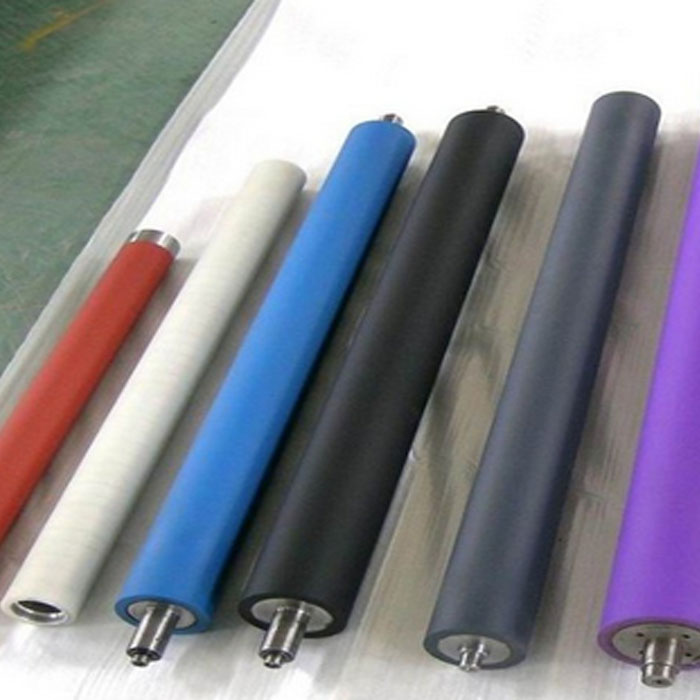
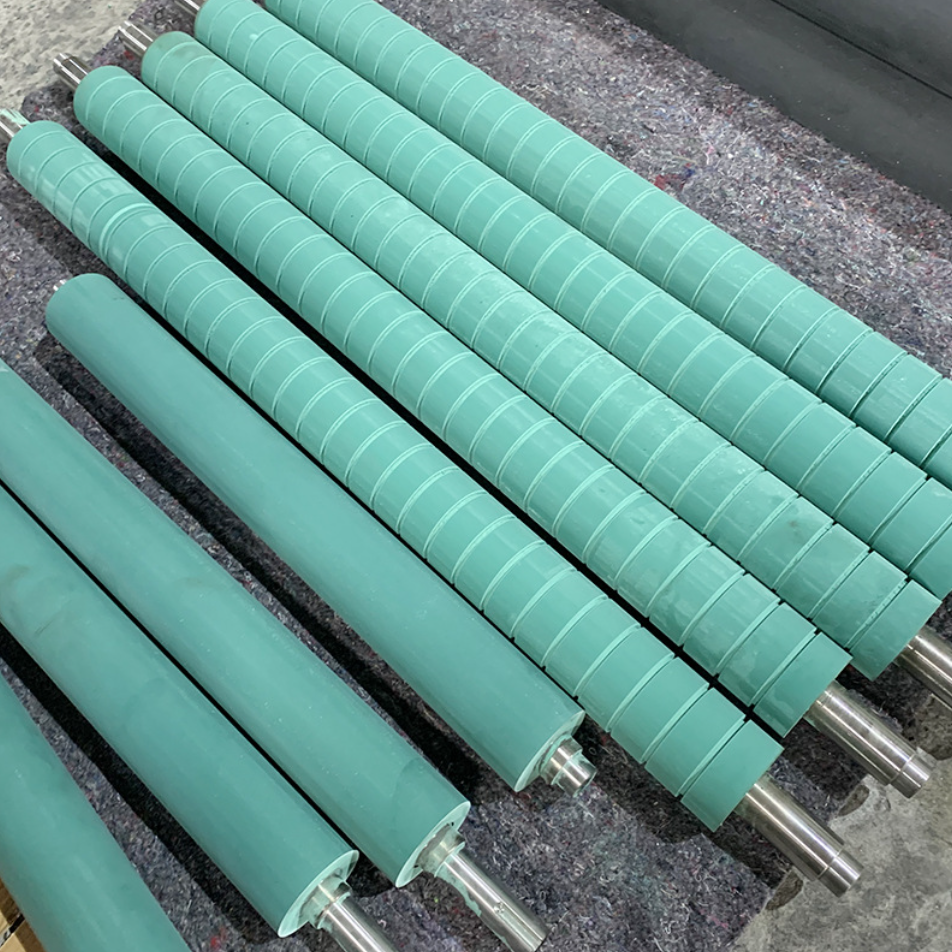
Different special properties of rubber rollers, such as heat resistance, oil resistance, solvent swelling resistance, etc. When the rubber roller is running, the gap between the two rollers will play a role. The gap size can be measured from the straight distance between the roller and the roller or between the surface and the surface. It must have the smallest roller moment and the strictest concentricity tolerance.
If the flatness and uniformity have been specified separately, the diameter tolerance of the rubber roller can be more or less relaxed. In order to ensure the accurate size and surface finish of the product, the grinding and finishing of the rubber roller are particularly important processes.
The performance requirements of rubber rollers with different functions can be roughly summarized as follows:
①Glue roller requires smooth surface and flatness, solvent and chemical resistance.
②The squeeze roller needs to have good toughness, wear resistance, chemical resistance and good heat resistance.
③The transfer rubber roller is required to have abrasion resistance and good toughness.
④The cushion rubber roller should have low heat build-up, good toughness and puncture resistance.
⑤The transmission rubber roller requires abrasion resistance, toughness and oil resistance, and requires low heat build-up.
When preparing the rubber roller, it is necessary to select the suitable raw rubber according to the requirements of the use conditions and the properties of the rubber material. The physical properties of the final rubber roller outer layer rubber can be further composed of a variety of reinforcing agents and plasticizers. adjust.
Performance requirements for rubber rollers
The rubber material of the outer layer of the rubber roller must have physical and mechanical properties that can meet the requirements of use. In addition to proper tensile strength, elasticity, abrasion resistance, and tear resistance, a particularly important property is hardness. Usually the biggest difference between rubber rollers for different purposes is the difference in the hardness of the outer layer of rubber. The lowest hardness rubber roller is only 6-10 Shore A degrees, and the highest hardness rubber roller reaches 100 Shore A degrees.
Under high-speed and high-pressure conditions, special attention should be paid to the heat build-up of the rubber material for the rubber rollers used, because the rubber rollers running under such conditions will convert the deformation and deflection of the rubber into the internal heat generation of the rubber. . A large amount of internal heat often damages the interface of the glue layer, especially when there are a lot of bubbles in the rubber roller, the temperature rise will completely destroy the glue layer, crack quickly and separate from the core. The amount of heat generated by the rubber layer depends on its deformation, the speed of deformation and the inherent heat-generating characteristics of the rubber itself. It is very important to choose a rubber formulation with as little heat as possible. First, choose a rubber with a low heat. At the same time, it is also necessary to note that the selected compounding agent type and amount also have a significant effect on the heat generation of the rubber. When the performance permits, try to reduce the thickness of the glue layer as much as possible, which will help the heat diffuse to the roll core and roll surface.
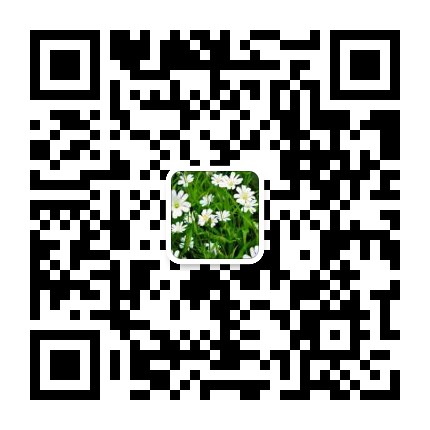
Post time: Jun-17-2021