Rubber rollers are common carton equipment accessories, and are often used in carton ink printing machines. They are also one of the necessary accessories. The rubber rollers will be made into the shape of a medium and high parabola, and the production height and hardness can be accurately calculated according to the needs of customers. , thickness, roller length, diameter and other requirements, let's further understand the main function of the lower rubber roller.
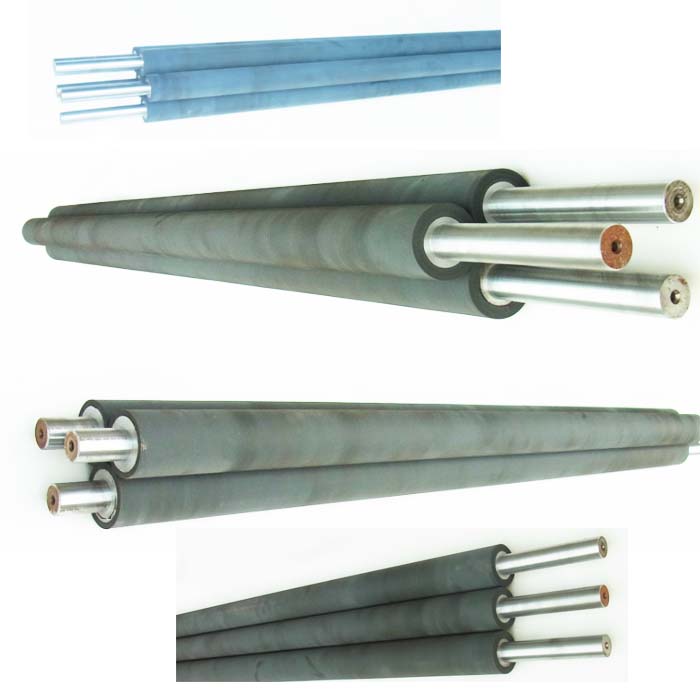
1. The rubber roller ensures the supply of ink in the ink printing machine. The rubber roller and the anilox roller cooperate with each other to achieve the function of "ink fountain", so that the ink can flow reasonably and supply ink.
2. The rubber roller is also the main player to spread the ink evenly as the ink layer. The rubber roller and the anilox roller squeeze and rotate each other, so that the ink is evenly spread and the excess ink is removed.
The rubber roller and anilox roller ink supply system can print large-area and thicker online stores, and adjust the hardness and speed of the rubber roller to achieve continuous printing of layered versions.
How does the surface structure of the printing roller affect printing? Its role is to transfer water and ink to the printing plate. The selection of rubber materials and the production process will affect the quality of the rubber roller. The quality of different rubber rollers determines the quality, effect and efficiency of printing. The surface roughness of the printing rubber roller is an important property that affects the transfer of ink and fountain solution by the rubber roller.
Therefore, surface roughness plays a crucial role in printing, it can accurately measure the amount of ink and water transferred, maintain the balance of ink and water, and the stability of ink transfer to ensure the stability of printing color. At the same time, it can separate the ink evenly in the form of an ink film and a water film to ensure smooth and continuous transmission of ink and fountain solution, and form the accumulation of ink and fountain solution to compensate for uneven defects caused by the transportation process. However, in the actual printing process, the rubber roller is often in contact with chemicals, and some residual impurities accumulate on the rubber surface of the rubber roller. Some of these residues can be cleaned with water or solvent, but a small amount of impurities still remain in the micropores on the rubber surface. bottom. These residues accumulate in the hole for a long time. Under the action of printing pressure and heat, the surface of the rubber roller will eventually lose its microporosity and wear out, resulting in glaze, that is, glaze phenomenon.
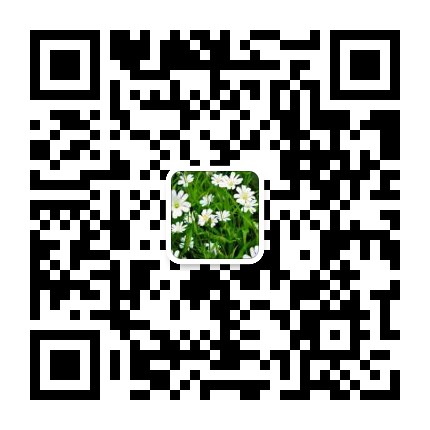
Post time: Apr-11-2022