Characteristics of polyurethane rubber rollers:
Use the slight elastic deformation of the rubber surface of the rubber shoe to adapt to the load and specific pressure without damaging the object itself.
It replaces metal parts in mechanical parts and plays the role of conduction, clamping and support.
Shock absorption, shock absorption, and noise reduction improve the working environment.
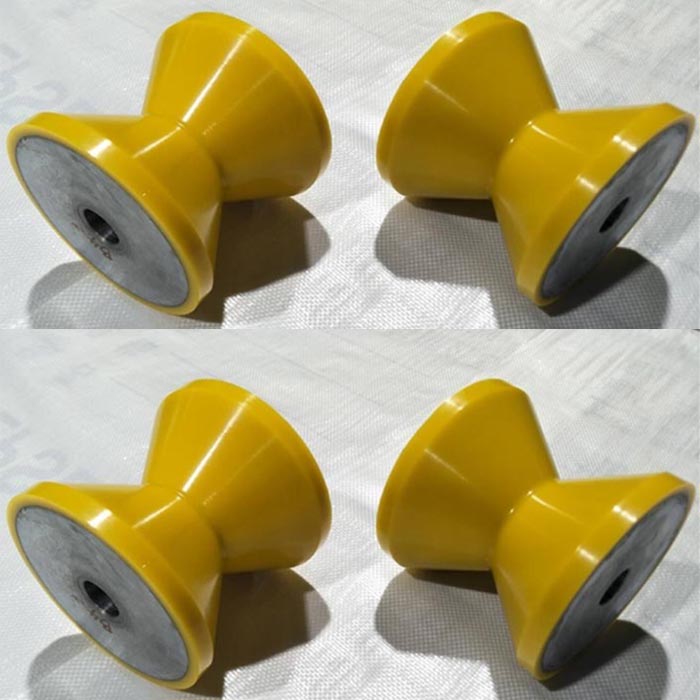
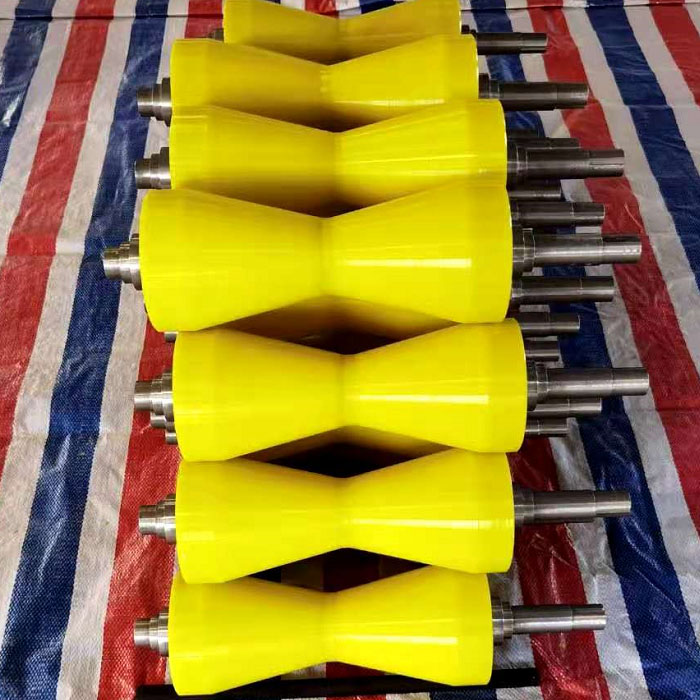
As an indispensable accessory of the offset printing machine, the rubber roller has a great influence on the printing quality of the product. It can be said that only good rubber rollers can print high-quality products. Therefore, how to use and maintain printing rubber rollers scientifically, correctly and reasonably is a production skill that printing operators should master. It is of great significance for improving production efficiency and ensuring printing quality.
1. Keep the surface of the rubber roller clean to improve its viscosity and achieve good ink transfer and distribution effects. In the printing process, in order to achieve uniform ink transfer and distribution, the surface of the colloid must maintain a certain viscosity. However, as the rubber roller is used for a long time, its surface will lose its adhesion with the loss of moisture. In addition, due to paper dust, paper wool and other properties, which affect the transfer of ink, it is also prone to uneven ink distribution. To make the rubber roller maintain a certain viscosity, prevent the ink from drying too fast and cause the rubber roller to crust, and control the amount of dry oil for the ink that needs to add dry oil. Generally speaking, the amount of resin ink and white dry oil should not exceed 5%; the amount of oil-based ink and white dry oil should not exceed 10%; the amount of red dry oil should be about 2%, so as not to affect the printing quality. In order to keep the rubber roller clean, the rubber roller should be cleaned at the appropriate time, but the impurities and paper dust on the colloid should be removed to improve the ink transfer performance.
2. It is necessary to place the rubber roller in a suitable position on the printer accurately and at a high speed to avoid damage and poor ink distribution caused by improper use. The proper position of the rubber roller is directly related to the uniformity of ink transfer and brushing, as well as the durability of the rubber roller. Therefore, the contact pressure between the ink rollers should be uniform and moderate. The contact pressure between the ink roller and the ink roller is too large. On the one hand, the rubber roller will be deformed under pressure, and the colloid will easily expand due to heat distribution. It is easy to become thin due to heat, which affects the quality of printing ink; on the other hand, it is easy to damage the rubber roller shaft head (bearing) or shaft hole. If the height adjustment of the inking roller is unsuitable, it will cause uneven ink distribution if it is adjusted too high. If the adjustment is too low, it is easy to scratch the colloid and aggravate the abrasion of the printing plate. Therefore, the inking roller should be adjusted to maintain a balance with the printing plate surface to ensure uniform ink brushing on the entire plate surface. For the contact between the high ink roller and the printing plate, generally a paper strip of about 40g can be placed on the printing plate. When the ink roller is rolled up, the paper strip can be pulled with a sense of pressure resistance.
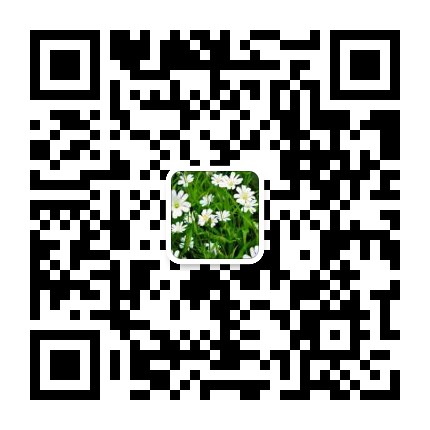
Post time: Jun-17-2021