How to improve the service life of the husking rubber roller, today we will explain some points in detail
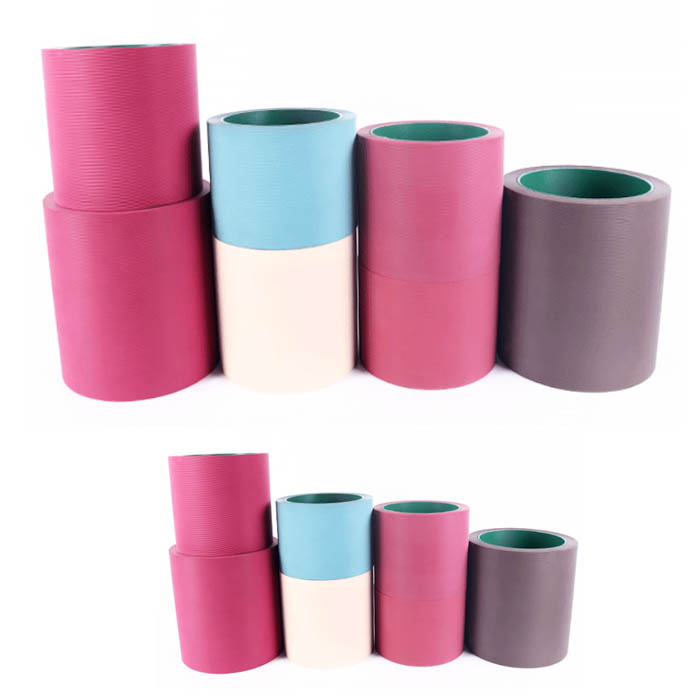
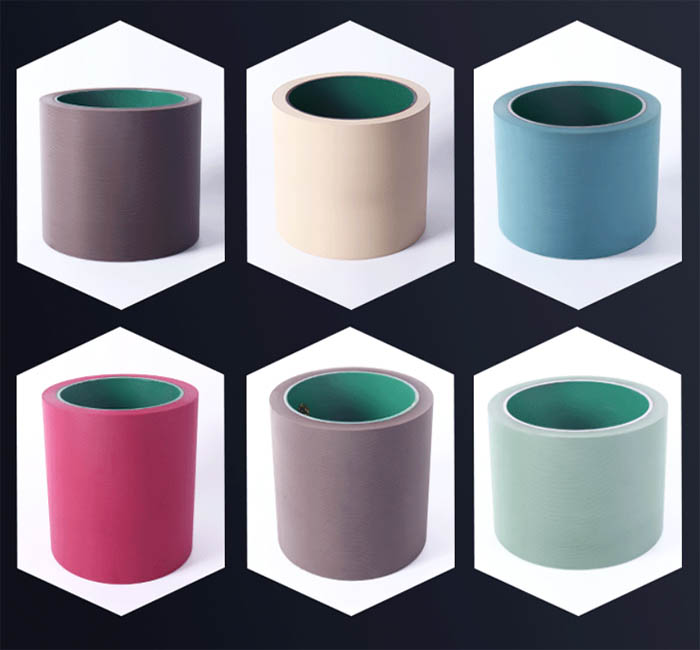
1. Reasonable selection of rubber rollers: For black, brown, white, Shore hardness 90o, 95o off rollers should be selected reasonably, according to the specific conditions of the rice variety, climatic conditions, seasons in the region, and reasonable matching, preferably fast. Choose rollers with higher hardness, slow rollers with lower hardness, and avoid using a single variety of rubber rollers. It is best to mix the first-generation cots with styrene-butadiene cots (SBR for short) and the fourth-generation cots with high wear resistance (Epdm for short).
2. Control the working temperature: the actual working hardness of the rubber roller is 78 o-82 o Shore when grinding rice. According to the measurement: the working temperature should be below 50℃ (when the working temperature is above 60℃, the hardness of the rubber roller will decrease by 4-8 degrees).
3. Use multiple rubber rollers alternately: This method can effectively improve the service life of the rubber rollers and the amount of rice milled. Its advantage is that each rubber roller has a working interval, which is conducive to eliminating fatigue stress, restoring the performance of the rubber compound, adjusting the line speed difference with different diameters, and effectively controlling the working temperature.
4. Strengthen the storage of rubber rollers: do a good job of anti-aging. The effective storage period of the rubber roller is stipulated as one year, so as to plan to purchase appropriate reserves and do a good job in the storage work. The specific storage requirements are as follows:
(1) Avoid direct sunlight and erosion by rain and snow, and be no less than 1.5 meters away from the heating device.
(2) It is forbidden to contact with substances that affect the quality of rubber such as acids, alkalis, salts, oils and organic solvents, and should be kept clean.
(3) The temperature of the storage warehouse should be kept between 10o-30o, and the relative temperature should be between 50o-80o.
(4) It should be rotated vertically, and other substances should not be placed horizontally or stacked. Do not strike to avoid deformation and damage.
Process conditions of paddy husk
The grain shelling process generally goes through three basic steps: extrusion, rubbing and tearing, and peeling. Among them, rubbing and tearing is the key to shelling. The size of rubbing and tearing depends on two important factors: one is the size of the friction force, and the friction force The size depends on the pressure between the two rollers; the second is the length of the relative action time of the reverse friction force on the grain, and the length of the action time depends on the relative speed of the two rollers, that is, the linear speed difference is related to . It is not difficult to see that the difference between the pressure between the rollers and the line speed is an important process parameter for rice husking. The correct selection of it not only directly affects the hulling rate, but also affects the consumption of rubber rollers.
General principles for selecting process parameters
The rice milling amount of the rubber roller is actually a comprehensive reflection of the hulling rate and the glue consumption. The two interact and restrict each other. The so-called optimal process state refers to both a high hulling rate and a Lower glue consumption is the general principle for selecting various process parameters.
1. Selection of line speed difference: Too large line speed difference can enhance the rubbing and tearing force and improve the shelling rate, but also increase the wear and power consumption of the rubber roller. The line speed difference is too small, the hulling rate is low, the loss is less, the back hulling increases, and the total rice milling amount is not high. It can be seen that the choice of the line speed difference must take into account the two aspects of the hulling rate and glue consumption, and one-sided pursuit of any one. All indicators are wrong. According to the actual operation experience, it is better to choose the line speed difference of 2.4-3 m/s. When the line speed difference is less than 2 meters, the shelling rate will drop significantly (the speed of the fast roll of the husker is 1350 rpm, and the speed of the slow roll is 1150 rpm. rev/sec; speed ratio is 1:1.17), the rubber roller is constantly worn out when the grain hulling machine is working, and its line speed difference is shrinking all the time, especially with fast rollers. In order to ensure a certain process effect, a certain line must be maintained. Speed difference, when the diameter of the fast roll is smaller than the diameter of the slow roll, the fast roll will be replaced immediately. Generally, the diameter of the fast roll is larger than that of the slow roll by 2-10mm. In actual work, the selection basis and factors of the line speed difference are various, such as the variety of rice, the thickness of the husk, the degree of compactness, the moisture content and the climatic conditions. Wait.
2. Selection of pressure between rollers: The pressure between rollers is also one of the key process parameters for the size of the rubbing and tearing force. On the roller type rice hulling machine, the pressure between rollers is adjusted by the weight of the pressed lump. In principle, it is easy to light and not heavy, and both sides are balanced. , the weight of pressing lumps can be appropriately increased with the gradual wear of the rubber rollers; for the husking machine with manual tightening rollers, the width of the distance between the rollers is appropriate to be equal to the thickness of the rice grains, generally 0.5 (indica) - 0.8 (japonica) mm. The principle of tight feeding and parallel feeding.
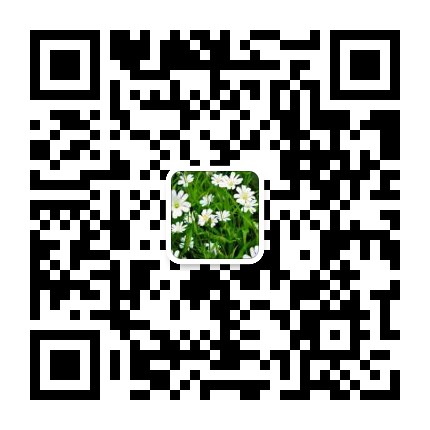
Post time: Jun-27-2022